Destylator przemysłowy to urządzenie służące do separacji składników cieczy na podstawie różnic w ich temperaturach wrzenia. Proces ten jest kluczowy w wielu gałęziach przemysłu, takich jak chemiczny, petrochemiczny, spożywczy czy farmaceutyczny. Destylacja polega na podgrzewaniu cieczy do momentu, gdy zaczyna ona parować, a następnie schładzaniu pary, co prowadzi do jej kondensacji i zbierania w postaci cieczy. W przemyśle stosuje się różne typy destylatorów, w tym destylatory prostokątne, kolumnowe oraz frakcyjne. Każdy z tych typów ma swoje specyficzne zastosowania oraz zalety. Destylatory kolumnowe są szczególnie popularne w procesach wymagających dużej efektywności separacji, ponieważ umożliwiają wielokrotne skraplanie i odparowywanie, co zwiększa czystość uzyskiwanych produktów.
Jakie są zastosowania destylatorów przemysłowych w różnych branżach
Destylatory przemysłowe znajdują szerokie zastosowanie w różnych branżach, co czyni je niezwykle ważnym elementem nowoczesnej produkcji. W przemyśle chemicznym destylacja jest wykorzystywana do oczyszczania surowców oraz produkcji różnych substancji chemicznych. Na przykład, wiele związków organicznych jest pozyskiwanych poprzez destylację z mieszanin reakcyjnych. W przemyśle petrochemicznym destylatory służą do rozdzielania frakcji ropy naftowej, co pozwala na uzyskanie paliw oraz innych produktów naftowych. Z kolei w branży spożywczej destylacja jest kluczowym procesem w produkcji alkoholi oraz olejków eterycznych. Dzięki temu można uzyskać czyste i skoncentrowane aromaty, które są wykorzystywane zarówno w przemyśle spożywczym, jak i kosmetycznym. W farmacji natomiast destylatory są używane do produkcji substancji czynnych oraz ich oczyszczania, co jest niezbędne dla zapewnienia jakości leków.
Jakie są rodzaje destylatorów przemysłowych i ich charakterystyka
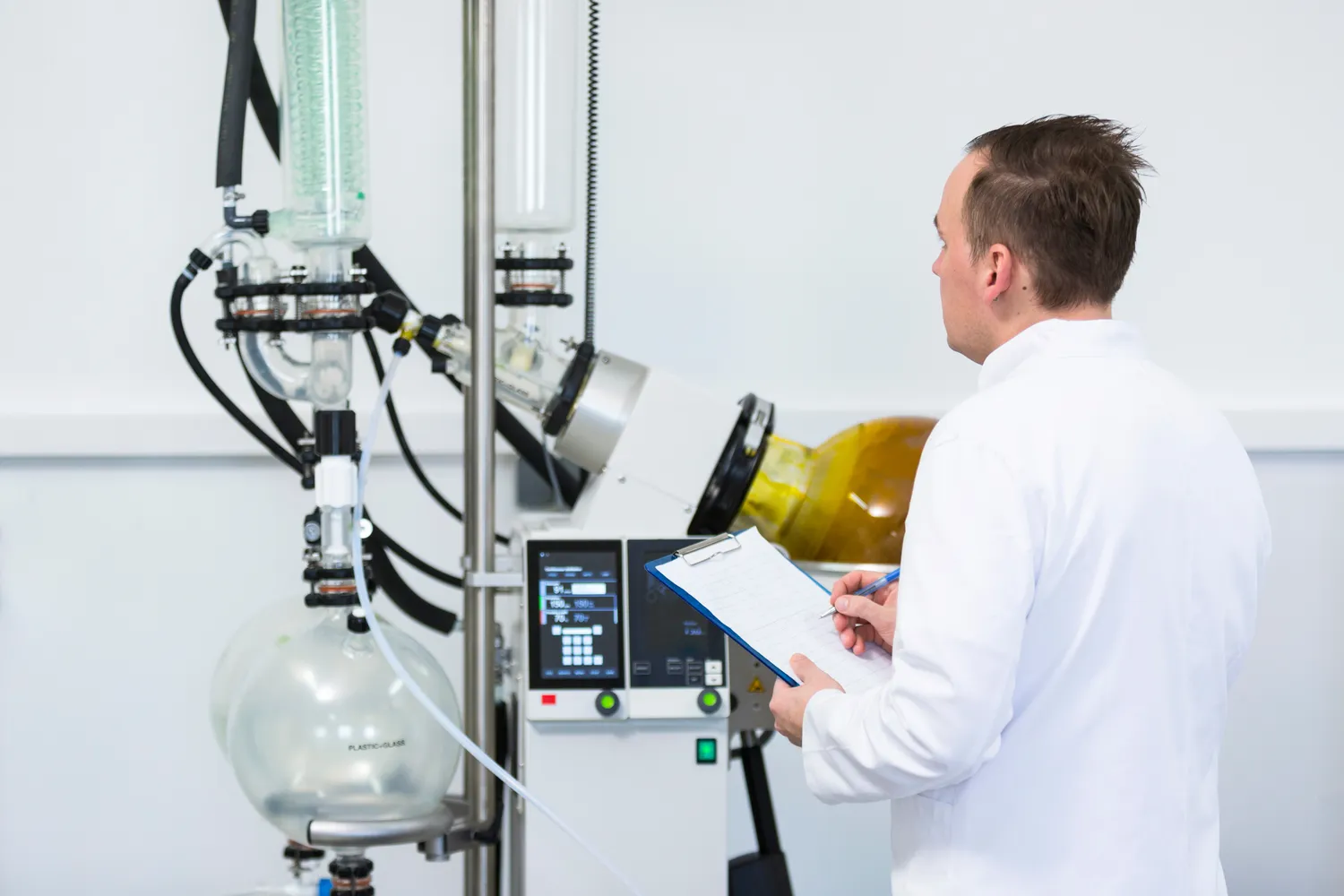
W przemyśle można spotkać wiele różnych typów destylatorów, które różnią się konstrukcją oraz przeznaczeniem. Najpopularniejsze z nich to destylatory prostokątne, kolumnowe oraz frakcyjne. Destylatory prostokątne charakteryzują się prostą budową i są często stosowane w małych zakładach produkcyjnych lub laboratoriach. Ich główną zaletą jest łatwość obsługi oraz niskie koszty eksploatacji. Z kolei destylatory kolumnowe są bardziej zaawansowane technologicznie i umożliwiają efektywną separację składników dzięki zastosowaniu kolumny z materiałem packingowym lub talerzowym. Tego typu urządzenia są idealne do procesów wymagających wysokiej czystości produktów końcowych. Destylatory frakcyjne natomiast pozwalają na jednoczesną separację wielu składników z mieszaniny, co czyni je niezwykle efektywnymi w przypadku skomplikowanych procesów chemicznych.
Jakie są kluczowe czynniki wpływające na wydajność destylacji
Wydajność procesu destylacji zależy od wielu czynników, które mogą znacząco wpłynąć na jakość i ilość uzyskiwanych produktów. Jednym z najważniejszych aspektów jest temperatura wrzenia poszczególnych składników mieszaniny. Im większa różnica między temperaturami wrzenia, tym łatwiejsza separacja składników. Kolejnym istotnym czynnikiem jest ciśnienie atmosferyczne; obniżenie ciśnienia może prowadzić do obniżenia temperatury wrzenia substancji, co może być korzystne w przypadku delikatnych związków chemicznych. Prędkość przepływu cieczy przez destylator również ma znaczenie; zbyt szybki przepływ może prowadzić do niedostatecznej separacji składników, podczas gdy zbyt wolny może obniżyć wydajność całego procesu. Dodatkowo właściwości fizykochemiczne substancji takie jak lepkość czy gęstość mogą wpływać na efektywność procesu destylacji.
Jakie są nowoczesne technologie stosowane w budowie destylatorów przemysłowych
Nowoczesne technologie mają ogromny wpływ na rozwój konstrukcji destylatorów przemysłowych, co przekłada się na ich wydajność oraz efektywność energetyczną. Współczesne urządzenia często wykorzystują zaawansowane materiały izolacyjne oraz systemy automatyzacji, które pozwalają na precyzyjne kontrolowanie parametrów pracy. Dzięki zastosowaniu technologii cyfrowych możliwe jest monitorowanie procesu w czasie rzeczywistym oraz dostosowywanie ustawień urządzenia do zmieniających się warunków pracy. Innowacyjne rozwiązania obejmują także wykorzystanie nanotechnologii do poprawy właściwości materiałów użytych w budowie kolumn czy wymienników ciepła. Dodatkowo coraz częściej stosuje się systemy odzysku ciepła, które pozwalają na zwiększenie efektywności energetycznej całego procesu poprzez ponowne wykorzystanie energii generowanej podczas destylacji.
Jakie są kluczowe aspekty bezpieczeństwa w pracy z destylatorami przemysłowymi
Bezpieczeństwo w pracy z destylatorami przemysłowymi jest niezwykle istotnym zagadnieniem, które wymaga szczególnej uwagi ze względu na potencjalne zagrożenia związane z obsługą tych urządzeń. Przede wszystkim, należy pamiętać o ryzyku związanym z wysokimi temperaturami oraz ciśnieniem, które mogą prowadzić do niebezpiecznych sytuacji, takich jak wybuchy czy pożary. Dlatego kluczowe jest stosowanie odpowiednich zabezpieczeń, takich jak zawory bezpieczeństwa oraz systemy monitorujące, które pozwalają na bieżąco kontrolować parametry pracy destylatora. Warto również zwrócić uwagę na materiały używane w budowie destylatorów; powinny one być odporne na korozję oraz wysokie temperatury, aby zminimalizować ryzyko awarii. Szkolenie pracowników w zakresie obsługi urządzeń oraz procedur awaryjnych jest kolejnym ważnym elementem zapewniającym bezpieczeństwo. Regularne przeglądy techniczne oraz konserwacja sprzętu również odgrywają kluczową rolę w utrzymaniu wysokiego poziomu bezpieczeństwa.
Jakie są koszty związane z zakupem i eksploatacją destylatorów przemysłowych
Koszty związane z zakupem i eksploatacją destylatorów przemysłowych mogą być znaczne, dlatego przed podjęciem decyzji o inwestycji warto dokładnie przeanalizować wszystkie aspekty finansowe. Cena zakupu destylatora zależy od jego typu, wielkości oraz zastosowanych technologii. Destylatory kolumnowe i frakcyjne zazwyczaj są droższe od prostokątnych ze względu na bardziej skomplikowaną konstrukcję i wyższą wydajność. Oprócz kosztu zakupu należy uwzględnić także wydatki związane z instalacją, uruchomieniem oraz szkoleniem personelu. Koszty eksploatacji obejmują zużycie energii, konserwację oraz ewentualne naprawy. Warto również pamiętać o kosztach surowców wykorzystywanych w procesie destylacji oraz o wpływie regulacji prawnych na koszty produkcji. W dłuższej perspektywie czasowej inwestycja w nowoczesne technologie może przynieść oszczędności dzięki zwiększonej efektywności energetycznej oraz mniejszym kosztom operacyjnym.
Jakie są różnice między destylacją prostą a frakcyjną
Destylacja prosta i frakcyjna to dwa podstawowe rodzaje procesów separacyjnych stosowanych w przemyśle, które różnią się zarówno zasadą działania, jak i zastosowaniem. Destylacja prosta jest najprostszą formą tego procesu i polega na podgrzewaniu cieczy do momentu jej wrzenia, a następnie skraplaniu pary w celu oddzielenia składnika o niższej temperaturze wrzenia od pozostałych substancji. Proces ten jest skuteczny jedynie wtedy, gdy różnica temperatur wrzenia składników jest znaczna. Z kolei destylacja frakcyjna to bardziej zaawansowany proces, który umożliwia separację wielu składników jednocześnie dzięki zastosowaniu kolumny frakcyjnej. W tym przypadku para przechodzi przez kolumnę, gdzie wielokrotnie skrapla się i odparowuje, co pozwala na uzyskanie wyższej czystości produktów końcowych. Destylacja frakcyjna jest szczególnie przydatna w przypadku mieszanin o niewielkich różnicach temperatur wrzenia, takich jak ropa naftowa czy mieszanki chemiczne.
Jakie są najnowsze osiągnięcia w dziedzinie destylacji przemysłowej
Najnowsze osiągnięcia w dziedzinie destylacji przemysłowej koncentrują się głównie na zwiększeniu efektywności energetycznej oraz poprawie jakości produktów końcowych. Jednym z innowacyjnych rozwiązań jest zastosowanie technologii membranowych, które pozwalają na separację składników bez konieczności podgrzewania cieczy. Dzięki temu proces staje się bardziej energooszczędny i przyjazny dla środowiska. Inne nowoczesne podejścia obejmują wykorzystanie sztucznej inteligencji do optymalizacji parametrów procesu destylacji oraz monitorowania stanu urządzeń w czasie rzeczywistym. Dzięki algorytmom uczenia maszynowego możliwe jest przewidywanie awarii oraz automatyczne dostosowywanie ustawień urządzenia do zmieniających się warunków pracy. Również rozwój materiałów nanostrukturalnych przyczynia się do poprawy efektywności procesów separacyjnych poprzez zwiększenie powierzchni kontaktu między fazami ciekłymi a gazowymi.
Jakie są wyzwania związane z przyszłością technologii destylacji przemysłowej
Przyszłość technologii destylacji przemysłowej wiąże się z wieloma wyzwaniami, które muszą zostać rozwiązane, aby zapewnić dalszy rozwój tej branży. Jednym z głównych problemów jest potrzeba zwiększenia efektywności energetycznej procesów produkcyjnych w obliczu rosnących cen energii oraz zaostrzających się norm ekologicznych. Firmy muszą inwestować w nowoczesne technologie oraz innowacyjne rozwiązania, aby ograniczyć zużycie energii i emisję gazów cieplarnianych. Kolejnym wyzwaniem jest konieczność dostosowania procesów produkcyjnych do zmieniających się potrzeb rynku oraz oczekiwań konsumentów dotyczących jakości produktów. W miarę jak rośnie zainteresowanie produktami ekologicznymi i naturalnymi, producenci będą musieli opracować nowe metody separacji składników, które będą spełniać te wymagania. Dodatkowo globalizacja rynku stawia przed firmami nowe wyzwania związane z konkurencją oraz koniecznością dostosowania się do lokalnych regulacji prawnych.
Jakie są perspektywy rozwoju rynku destylatorów przemysłowych
Perspektywy rozwoju rynku destylatorów przemysłowych wyglądają obiecująco, zwłaszcza w kontekście rosnącego zapotrzebowania na produkty chemiczne oraz paliwa alternatywne. W miarę jak świat staje przed wyzwaniami związanymi ze zmianami klimatycznymi i ograniczonymi zasobami naturalnymi, coraz większy nacisk kładzie się na poszukiwanie efektywnych metod produkcji oraz recyklingu surowców. Destylatory przemysłowe będą odgrywać kluczową rolę w procesach przetwarzania surowców wtórnych oraz produkcji biopaliw, co stwarza nowe możliwości dla producentów tych urządzeń. Dodatkowo rozwój technologii cyfrowych otwiera nowe horyzonty dla automatyzacji procesów produkcyjnych oraz ich monitorowania w czasie rzeczywistym, co może przyczynić się do zwiększenia wydajności i redukcji kosztów operacyjnych.