Budowa maszyn produkcyjnych to skomplikowany proces, który wymaga uwzględnienia wielu kluczowych elementów. W pierwszej kolejności należy zwrócić uwagę na konstrukcję mechaniczną maszyny, która musi być solidna i trwała, aby wytrzymać intensywne użytkowanie w warunkach przemysłowych. Elementy takie jak ramy, podzespoły mechaniczne oraz systemy napędowe odgrywają fundamentalną rolę w zapewnieniu stabilności i efektywności pracy maszyny. Kolejnym istotnym aspektem jest automatyzacja procesów, która pozwala na zwiększenie wydajności produkcji oraz redukcję błędów ludzkich. W tym kontekście zastosowanie nowoczesnych technologii, takich jak robotyka czy sztuczna inteligencja, staje się coraz bardziej powszechne. Nie można również zapomnieć o systemach sterowania, które umożliwiają precyzyjne zarządzanie pracą maszyny oraz monitorowanie jej stanu.
Jakie materiały są wykorzystywane w budowie maszyn produkcyjnych
W budowie maszyn produkcyjnych wykorzystuje się różnorodne materiały, które mają kluczowe znaczenie dla ich funkcjonalności i trwałości. Najczęściej stosowanym materiałem jest stal, ze względu na swoje właściwości mechaniczne oraz odporność na uszkodzenia. Stal nierdzewna znajduje zastosowanie w maszynach, które pracują w trudnych warunkach lub wymagają wysokiej higieny, jak w przemyśle spożywczym czy farmaceutycznym. Oprócz stali, coraz częściej używa się także tworzyw sztucznych, które charakteryzują się niską wagą i odpornością na korozję. Materiały kompozytowe stają się popularne w kontekście nowoczesnych rozwiązań inżynieryjnych, oferując połączenie lekkości z wysoką wytrzymałością. W przypadku elementów ruchomych ważne jest również zastosowanie odpowiednich smarów i powłok ochronnych, które zmniejszają tarcie i zużycie materiałów.
Jakie technologie są stosowane w budowie maszyn produkcyjnych
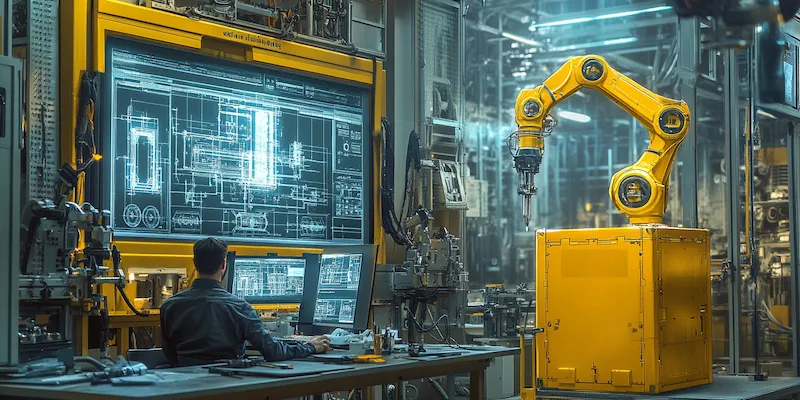
W dzisiejszych czasach budowa maszyn produkcyjnych opiera się na zaawansowanych technologiach, które znacząco zwiększają ich wydajność oraz funkcjonalność. Jedną z najważniejszych innowacji jest automatyzacja procesów produkcyjnych, która pozwala na zminimalizowanie udziału człowieka w rutynowych zadaniach. Roboty przemysłowe stały się nieodłącznym elementem nowoczesnych linii produkcyjnych, wykonując skomplikowane operacje z dużą precyzją i szybkością. Ponadto technologie takie jak Internet rzeczy (IoT) umożliwiają zdalne monitorowanie i zarządzanie maszynami, co przekłada się na lepsze planowanie konserwacji oraz szybsze reagowanie na awarie. Wykorzystanie symulacji komputerowych podczas projektowania maszyn pozwala na optymalizację ich konstrukcji jeszcze przed rozpoczęciem produkcji. Również druk 3D zyskuje na znaczeniu w kontekście prototypowania i wytwarzania części zamiennych, co przyspiesza proces rozwoju nowych rozwiązań technologicznych.
Jakie są etapy procesu budowy maszyn produkcyjnych
Proces budowy maszyn produkcyjnych składa się z kilku kluczowych etapów, które są niezbędne do stworzenia funkcjonalnego i wydajnego urządzenia. Pierwszym krokiem jest faza projektowania, która obejmuje zarówno koncepcję ogólną maszyny, jak i szczegółowe rysunki techniczne poszczególnych komponentów. Na tym etapie inżynierowie muszą uwzględnić wszystkie wymagania dotyczące wydajności oraz bezpieczeństwa pracy maszyny. Następnie przechodzi się do wyboru odpowiednich materiałów oraz technologii produkcji, co ma kluczowe znaczenie dla późniejszej eksploatacji urządzenia. Kolejnym etapem jest montaż poszczególnych elementów maszyny oraz przeprowadzenie testów funkcjonalnych, które mają na celu upewnienie się o poprawności działania wszystkich systemów. Po zakończeniu testów następuje faza wdrożenia maszyny do użytku oraz szkolenie personelu obsługującego urządzenie.
Jakie są najczęstsze problemy w budowie maszyn produkcyjnych
Budowa maszyn produkcyjnych wiąże się z wieloma wyzwaniami, które mogą prowadzić do problemów na różnych etapach procesu. Jednym z najczęstszych problemów jest niewłaściwe zaprojektowanie maszyny, co może skutkować jej niską wydajnością lub awaryjnością. Często zdarza się, że inżynierowie nie uwzględniają wszystkich warunków pracy, co prowadzi do nieprzewidzianych usterek. Kolejnym istotnym problemem jest wybór niewłaściwych materiałów, które mogą nie spełniać wymagań dotyczących wytrzymałości czy odporności na korozję. W przypadku maszyn, które pracują w trudnych warunkach, jak na przykład w przemyśle chemicznym, zastosowanie niewłaściwych materiałów może prowadzić do szybkiego zużycia i konieczności kosztownych napraw. Problemy mogą również wystąpić podczas montażu, gdy elementy nie są odpowiednio dopasowane lub zainstalowane. Niezgodności w montażu mogą prowadzić do drgań, hałasu oraz obniżenia efektywności maszyny.
Jakie są przyszłe trendy w budowie maszyn produkcyjnych
Przyszłość budowy maszyn produkcyjnych zapowiada się niezwykle interesująco dzięki dynamicznemu rozwojowi technologii oraz zmieniającym się wymaganiom rynku. Jednym z kluczowych trendów jest rosnąca automatyzacja procesów produkcyjnych, która pozwala na zwiększenie wydajności oraz redukcję kosztów operacyjnych. Wprowadzenie robotów współpracujących, które mogą pracować obok ludzi bez potrzeby stosowania barier ochronnych, staje się coraz bardziej powszechne. Kolejnym ważnym trendem jest integracja systemów IoT, które umożliwiają zbieranie danych w czasie rzeczywistym oraz analizę ich w celu optymalizacji procesów produkcyjnych. Dzięki temu możliwe jest przewidywanie awarii i planowanie konserwacji jeszcze przed wystąpieniem problemu. Również rozwój sztucznej inteligencji ma ogromny wpływ na budowę maszyn produkcyjnych, umożliwiając tworzenie bardziej zaawansowanych systemów sterowania oraz analizy danych. W kontekście zrównoważonego rozwoju coraz większą rolę odgrywa również ekologia – projektanci maszyn starają się wykorzystywać materiały przyjazne dla środowiska oraz minimalizować zużycie energii podczas pracy urządzeń.
Jakie są kluczowe zasady bezpieczeństwa w budowie maszyn produkcyjnych
Bezpieczeństwo w budowie maszyn produkcyjnych jest jednym z najważniejszych aspektów, który należy uwzględnić na każdym etapie procesu projektowania i eksploatacji urządzeń. Kluczową zasadą jest przestrzeganie norm i standardów bezpieczeństwa, które regulują kwestie związane z konstrukcją i użytkowaniem maszyn. Inżynierowie muszą zapewnić odpowiednie zabezpieczenia mechaniczne oraz elektroniczne, które chronią operatorów przed potencjalnymi zagrożeniami. Ważne jest również przeprowadzanie regularnych szkoleń dla personelu obsługującego maszyny, aby byli świadomi ryzyk związanych z ich pracą oraz umieli reagować w sytuacjach awaryjnych. Kolejnym istotnym elementem jest stosowanie odpowiednich procedur konserwacji i serwisowania maszyn, co pozwala na utrzymanie ich w dobrym stanie technicznym i minimalizuje ryzyko awarii. Należy także zwrócić uwagę na ergonomię stanowisk pracy – dobrze zaprojektowane miejsce pracy zmniejsza ryzyko kontuzji i poprawia komfort operatora.
Jakie są różnice między różnymi typami maszyn produkcyjnych
Różnorodność maszyn produkcyjnych sprawia, że każda z nich ma swoje unikalne cechy oraz zastosowania. Wśród najpopularniejszych typów można wyróżnić maszyny skrawające, formujące oraz montażowe. Maszyny skrawające są używane do obróbki materiałów poprzez usuwanie nadmiaru materiału za pomocą narzędzi skrawających – są one kluczowe w przemyśle metalowym i mechanicznym. Z kolei maszyny formujące służą do nadawania kształtu materiałom poprzez procesy takie jak tłoczenie czy gięcie – znajdują zastosowanie głównie w przemyśle tworzyw sztucznych i blacharskim. Maszyny montażowe natomiast zajmują się łączeniem różnych komponentów w jedną całość – są niezbędne w branży elektronicznej oraz motoryzacyjnej. Każdy typ maszyny charakteryzuje się innymi wymaganiami dotyczącymi konstrukcji oraz technologii produkcji, co wpływa na ich budowę i funkcjonalność.
Jakie są koszty związane z budową maszyn produkcyjnych
Koszty związane z budową maszyn produkcyjnych mogą być znaczne i zależą od wielu czynników, takich jak skomplikowanie projektu, wybór materiałów czy zastosowane technologie. W pierwszej kolejności należy uwzględnić koszty projektowania, które obejmują wynagrodzenia dla inżynierów oraz wydatki związane z oprogramowaniem CAD czy symulacjami komputerowymi. Następnie pojawiają się koszty zakupu materiałów – ceny stali czy tworzyw sztucznych mogą znacznie się różnić w zależności od jakości i dostawcy. Kolejnym istotnym elementem są koszty produkcji i montażu, które obejmują zarówno wynagrodzenia dla pracowników fabrycznych, jak i wydatki związane z użyciem specjalistycznego sprzętu czy narzędzi. Po zakończeniu budowy należy również uwzględnić koszty testowania maszyny oraz jej ewentualnej modyfikacji przed wdrożeniem do użytku.
Jakie są zalety nowoczesnych rozwiązań w budowie maszyn produkcyjnych
Nowoczesne rozwiązania w budowie maszyn produkcyjnych przynoszą szereg korzyści zarówno dla producentów, jak i dla samych użytkowników tych urządzeń. Przede wszystkim nowoczesne technologie pozwalają na zwiększenie wydajności procesów produkcyjnych poprzez automatyzację wielu rutynowych działań. Dzięki zastosowaniu robotyki i sztucznej inteligencji możliwe jest osiągnięcie wyższej precyzji oraz szybkości działania maszyn, co przekłada się na lepszą jakość produktów końcowych. Ponadto nowoczesne maszyny często charakteryzują się mniejszym zużyciem energii oraz surowców dzięki zastosowaniu innowacyjnych rozwiązań konstrukcyjnych i technologicznych. To nie tylko wpływa pozytywnie na koszty operacyjne przedsiębiorstw, ale również przyczynia się do ochrony środowiska naturalnego poprzez ograniczenie emisji CO2 oraz zmniejszenie ilości odpadów przemysłowych. Również łatwość integracji nowoczesnych systemów zarządzania produkcją sprawia, że przedsiębiorstwa mogą lepiej monitorować swoje procesy oraz podejmować decyzje oparte na danych analitycznych.